Arc flash is a sudden, explosive release of energy from an...
ReadIn the high-stakes environment of oil and gas, electrical system reliability is not only a matter of profit, but a critical component of safety and environmental protection. The financials of the oil and gas sector are highly influenced by the continuity of its operations – which are inherently complex and hazardous –, so any interruption in the electrical system can lead to significant production losses, safety incidents, and environmental disasters. This article explores why oil and gas operators must prioritize electrical reliability and presents a real-life study case where improvements in the electrical system of a massive oil field in South America generated substantial dividends. It also identifies common challenges and outlines effective solutions to enhance system robustness.
The importance of electrical reliability in oil and gas.
The US department of energy, in its Second Installment of the Quadrennial Energy Review of the US Department of Energy, 2017; indicates that electricity is at the heart of all critical infrastructure of the nation, including oil and natural gas (see Figure 1). Electrical systems in oil and gas facilities power a vast majority of operations, from drilling rigs to production wells, processing, and shipping facilities. These systems -which in some cases are remote- must operate flawlessly in environments which are often harsh, under extreme conditions of temperature, corrosion, humidity, weather, and exposed to the influence of wildlife. On the other hand, resources for timely maintenance are limited, and power quality may fall short of expectations. These aspects, combined or individually, could impact the continuity of electrical supply to the oil field, directly resulting in down production. Unplanned power outages not only lead to financial losses, but can also cause safety incidents, oil spills and gas leaks.
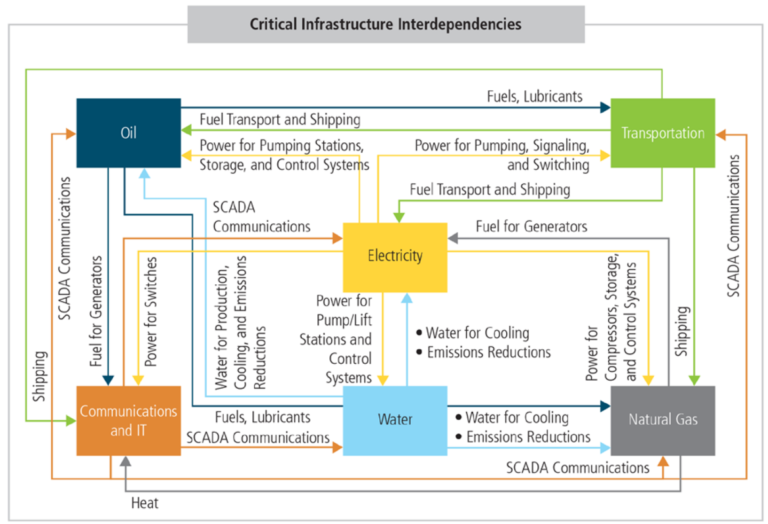
A study case.
This study case, where Altus Dexter engineers played a pivotal role, highlights the importance of oil field electrical reliability, showing how substantial improvements can be achieved with relatively small capital expenses, provided the right expertise and technology is applied.
In the mid 2000s, a massive oil field in South America was losing 0.4 MM barrels of oil per year – about 1% of its 37 million barrels produced annually – due to poor electrical system reliability. The operation depended on hundreds of miles of overhead power lines, and most of its hundreds of producing oil wells and processing equipment were driven by fragile variable frequency drives. Interestingly, the area is among the most active in the world for thunderstorms and lightning strikes, and it also hosts a biodiverse farmland where massive birds thrive in quantity and variety. Figure 2 provides a few images that resemble how the study case field looks.
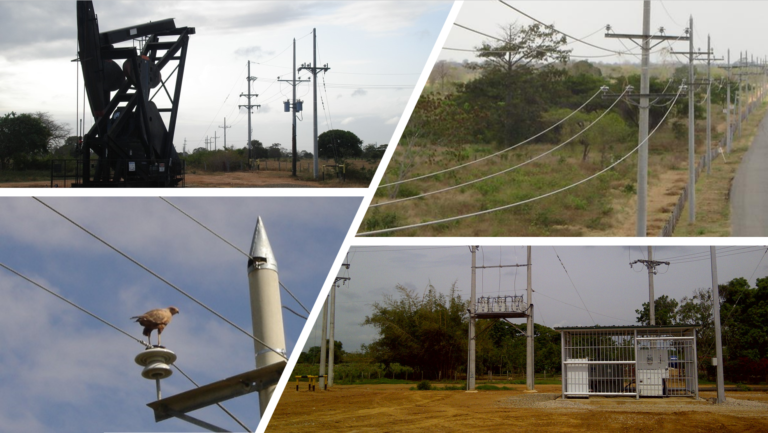
A team of talented engineers got to work, and based on the Pareto principle determined that more than 80% of this reliability problem was driven by less than 20% of the causes, which in this case included:
- Poor grounding, and insufficient overvoltage arresting capacity of the overhead lines.
- Poor ride through and overvoltage withstand capability at the utilization voltage level.
- Lack of single-phase tripping and reclosing in power distribution network.
After meticulous engineering and decision analysis, the team identified several key improvements and technologies to be applied to the power system. These were aimed at mitigating the identified causes to the greatest practical extent, while minimizing the amount of capital investment required to achieve this goal.
Among these improvements, a significant portion of the capital resources was allocated to enhancing the overhead distribution system: improving grounding, enhancing surge arresting capacity, and implementing wildlife deterrents. However, the most critical improvement was the adoption of what was then a relatively new technology: single-phase reclosing for overhead distribution networks. This innovation, combined with enhancements in ride-through capabilities and voltage surge suppression at the utilization voltage level, rendered the system virtually immune to more than 85% of the events that otherwise could have negatively impacted production continuity.
The results were remarkable, and the financial gains exceeded by several folds the investment. Within a few years, the implementation of these electrical reliability improvements drastically reduced production downtime attributable to electrical system reliability by more than 80% annually. A chart that resembles the evolution of these results is shown in Figure 3.
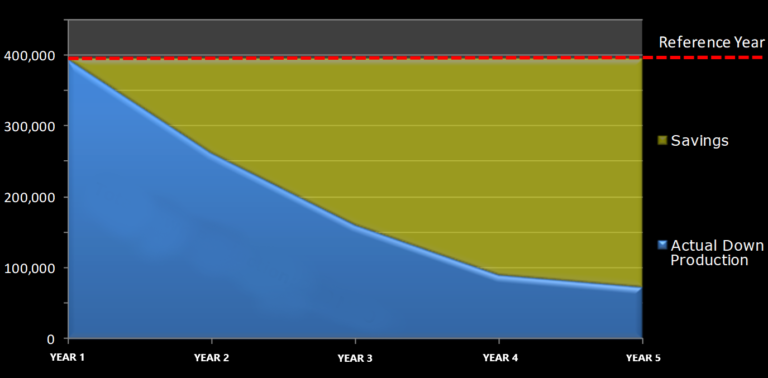
Common challenges to electrical reliability.
Beyond the ideas discussed for the specific circumstances of the study case, electrical reliability challenges in the oil field can be broadly generalized as follows:
- Harsh environmental conditions: exposure to extreme weather, corrosive substances, fluctuating temperatures, and wildlife can degrade electrical components, leading to failures.
- Equipment wear and tear: continuous operation and exposure to harsh conditions accelerate the wear and tear of electrical equipment, necessitating regular maintenance and updates.
- Power quality issues: oil and gas operations often rely on power from remote or unstable grids, subject to transients and harmonic distortion that can damage sensitive electrical equipment.
- Complex systems integration: modern oil and gas facilities feature sophisticated integration of various systems, where a failure in one can cascade, affecting the entire operation.
- Human error: improper installation, maintenance, or operation of electrical systems can lead to failures, highlighting the need for adequate training and protocols.
Solutions for enhanced electrical reliability
Fortunately, the appropriate combination of skills, experience and resources can both produce reliable electrical systems from conception or revert poor reliability in already existing systems. While each case demands a unique approach and specific analyses are always essential, there are general solutions that typically lead to satisfactory reliability outcomes. These include:
- Recurrent electrical system diagnosis and analysis: by regularly assessing and analyzing the performance of the electrical system, deviations can be detected, and proactive measures can be taken to guarantee appropriate levels of reliability.
- System redundancy: design new systems (or improve existing ones) with redundancy in mind, so critical components can continue operating even when faults and events occur.
- Robust design and quality equipment: design and invest in high-quality electrical components, properly rated for harsh environments, and ensure that the systems can accommodate upgrades and are maintainable.
- Preventive and predictive maintenance: implement a comprehensive maintenance strategy that includes regular inspections, testing, condition monitoring, and preventive action, to anticipate failures before they occur or diminish the likelihood of occurrence.
- Power quality management: use power monitoring equipment to guarantee systems are fed with appropriate power quality, and conditioning equipment like uninterruptible power supplies (UPS), ride through and transient protection to safeguard against voltage fluctuations and ensure steady operation.
- Training and safety protocols: enhance operator and maintainer training on the proper use and maintenance of electrical systems, and establish strict safety protocols to minimize human error.
Key takeaways.
Understanding the specific challenges that affect electrical reliability in the oil and gas industry, and implementing solutions backed by the right combination of engineering experience, skills, decision analysis, and technology, can prevent or reverse poor electrical reliability performance. This enables operators to ensure their facilities run smoothly, safely, and sustainably. Prioritizing electrical system reliability not only safeguards the bottom line but also ensures the safety of workers and the environment, highlighting its critical importance in the oil and gas sector.
This article is designed to serve as a comprehensive guide for oil and gas operators seeking to enhance the reliability of their electrical systems. By emphasizing system diagnosis and analysis, redundancy, robust design, preventive and predictive maintenance, power quality management, and operator training, facilities can mitigate risks, minimize downtime, and guarantee continuous, safe operations.
At Altus Dexter, we possess the expertise to navigate electrical system reliability in oil and gas facilities, offering customized solutions that align with both the unique operational demands and the electrical characteristics of our clients’ systems. Our capacity to address reliability challenges and manage complex systems is backed by a team of seasoned professionals committed to utilizing cutting-edge technology. With a proven track record of success in improving oil field reliability, Altus Dexter stands as your capable and qualified partner, ensuring that your electrical system is robust and dependable. We invite you to connect with us to benefit from our vast experience in oil and gas reliability, positioning your operation for success and sustainability.
Recommended citation.
Pineda, F., “Electrical Reliability in Oil and Gas: A Study Case”. Website article (2024). Altus Dexter. www.altusdexter.com
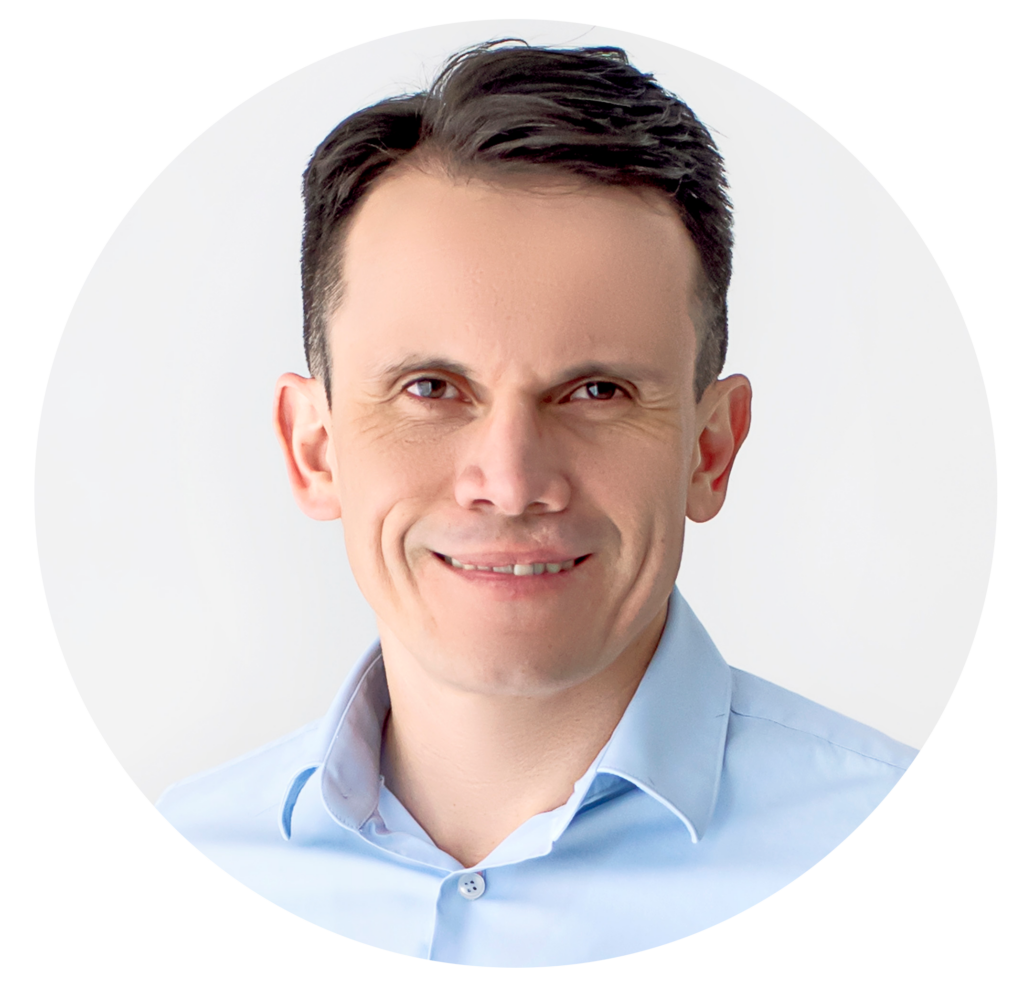
About the author
Fabian Pineda, P.E., is the Founder and Managing Director of Altus Dexter. He has extensive experience in project management, design, operation, reliability, and maintenance of electrical systems for industrial, oil, gas and offshore applications.
We also recommend
Electrical Reliability in Oil and Gas: A Study Case
In the high-stakes environment of oil and gas, electrical system reliability...
ReadCONTACT US
- (832) 773-1194
- info@altusdexter.com